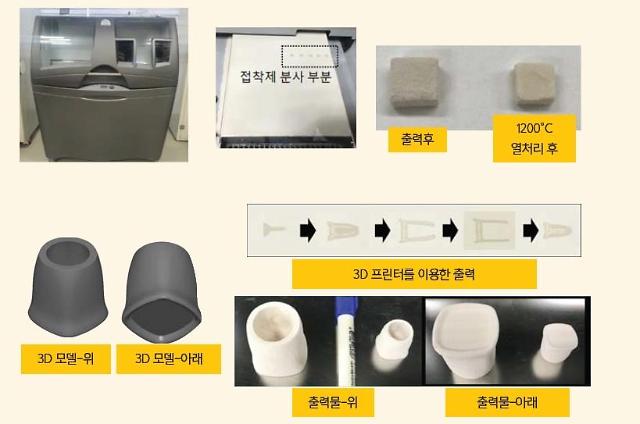
[Courtesy of KIGAM]
SEOUL -- 3D printing, or additive manufacturing, refers to a variety of processes in which material is deposited, joined or solidified under computer control to create a three-dimensional object. Materials such as plastics, liquids or powder grains being fused together layer by layer. Multi-material 3D printing allows the objects of complex and heterogeneous arrangements to be manufactured using a single printer.
Plastic items, powdered materials, metal and ceramic materials are widely used for 3D printing. Natural minerals are cheaper and easier to process than traditional ceramic raw materials. The Korea Institute of Geoscience and mineral resources (KIGAM) said its research team led by Seo Joo-beom has developed a technology that uses natural minerals with low manufacturing cost, excellent texture, high heat resistance, and chemical resistance as raw materials.
"As the implementation of advanced IT and AI technologies gained speed, the need for new 3D printing materials with structural stability and eco-friendliness is being raised in various ways," Seo said in a statement on October 5. "If natural minerals are used, they can be used in various ways not only for high-quality household goods close to our daily lives, but also for the production of a small variety of sophisticated high-tech products."
Seo has conducted research to develop natural minerals used in ceramic manufacturing as raw materials for binder jetting 3D printers. Binder Jetting is an additive manufacturing process and uses metals, sand, and ceramics. It is used in various applications such as low-cost 3D printing.
Seo's team secured optimized complex technology in consideration of the characteristics of individual minerals and evaluated various materials that can act as adhesives for the binding of spherical particles.
The research team implemented round particles with an average size of 45 micrometers (μm) by mixing crushed individual minerals at a specific ratio and then grinding them again to uniformly aggregate them, the institute said, adding that the fluidity of particles within a binder jetting 3D printer enabled additive manufacturing. Researchers found that heat treatment at high temperatures not only increases the strength of the output but also maintains the basic shape.
Copyright ⓒ Aju Press All rights reserved.