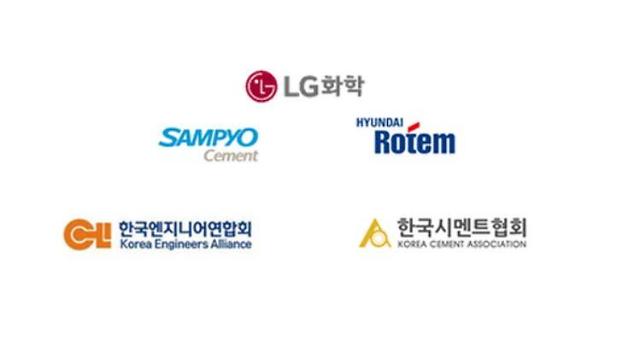
[Courtesy of LG Chem]
Burning waste plastics produces chlorine dust, a byproduct that cannot be recycled. Chlorine components attached to the walls of cement preheaters also reduce the utilization of production facilities. LG Chem tied up with Sampyo Cement, Hyundai Rotem, the Korea Cement Association and the Korea Engineers Alliance (KEA) to establish a virtuous cycle ecosystem of resources.
LG Chem, a chemical unit of LG Group, said it would provide technologies to prevent chlorine from attaching to the inside of furnaces and improve the stability of chlorine dust resource facilities. The company will develop high-value-added products such as potassium hydroxide and potassium carbonate by increasing the purity of potassium chloride, which relies on imports.
"With our partners in the waste plastic resource project, we will create various business models by combining the roles that each company plays well," Lee Ho-woo, general manager of sustainability at LG Chem's petrochemical business division, said in a statement on June 30.
Hyundai Rotem, a subsidiary of South Korea's Hyundai auto group, will use chlorine dust for the production of potassium chloride, which is used as a fertilizer or in medicine, scientific applications and food processing. It would provide chlorine dust treatment facilities and potassium chloride production lines to cement plants.
Sampyo Cement, a leading cement and concrete company in South Korea, promotes zero waste landfills by optimizing the operation of carbon dioxide mineralization and evaporation concentration for the production of potassium chloride. The Korea Cement Association is in charge of expanding resource recovery technology from waste plastics to the entire cement industry.