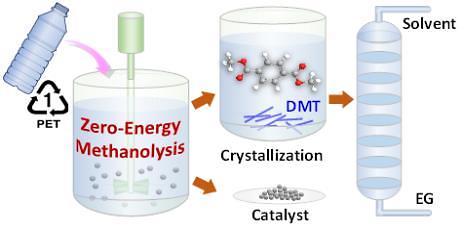
[Courtesy of the Korea Research Institute of Chemical Technology]
The Korea Research Institute of Chemical Technology (KRICT) said that its research team has developed a depolymerization technology that can completely decompose waste polyethylene terephthalate (PET) bottles and polyester fibers without excessive energy consumption. It is a multi-purpose eco-friendly material manufacturing method that can flexibly cope with changes in raw material prices or market demand.
"The conventional method which decomposed discarded plastics at about 250 degrees Celsius generated a large amount of carbon emissions and by-products," said KRICT's researcher Cho Joung-mo. "We developed a technology to create higher-value-added monomers using dimethyl terephthalate. It is a technology that can upcycle the manufactured products through methanolysis into high value-added monomers."
Methanolysis is a chemical pathway for depolymerizing PET plastic waste into monomeric feedstock, which can be utilized as a starting component to produce polymer materials. Conventional methanolysis requires a high reaction temperature under high pressure.
Cho's team has developed a low-energy catalytic route for methanolysis to convert PET resin to dimethyl terephthalate. Potassium carbonate, which is an inexpensive and nontoxic salt, was used as a catalyst. PET resins were completely decomposed into monomers within 24 hours.
For commercialization, the technology has been transferred to Renew System, a waterproofing solution company that will manufacture renewable monomers that can replace petrochemical-based plastic raw materials and use it for a high value-added additive raw material for special plastic synthesis.