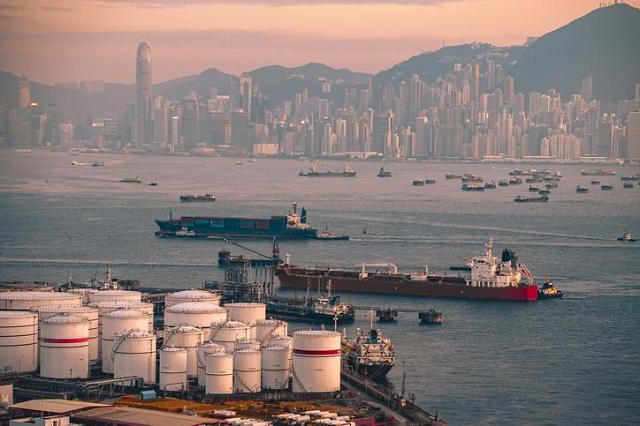
[Gettyimages Bank]
SEOUL -- A South Korean project to produce a commercially viable liquefied hydrogen fuel tank for ships appeared to have made quick progress after a prototype won preliminary approval from a domestic maritime classification society, based on design innovation and new cryogenic materials. Developers aim to transfer related technologies to shipbuilders by 2025.
Hydrogen is extremely flammable when it is mixed with very small amounts of air. The liquefaction of hydrogen requires cooling to a temperature of minus 253 degrees Celsius and subsequent storage in cryogenic containers. The advantage of liquefied hydrogen is its high density compared to compressed gas, which means that more energy can be contained in a given volume for easy transportation.
Amid growing demands for eco-friendly ships to cope with global economic recovery and environmental regulations, South Korea has accelerated the development of hydrogen-powered ships. A joint project led by the state-funded Korea Research Institute of Ships and Ocean Engineering (KRISO) was launched in September 2021 to develop a maritime liquefied hydrogen fuel tank. The project aims to test-produce a fuel tank for small ships before embarking on the development of tanks for large vessels.
The prototype of a 400kg-class tank secured approval in principle (AIP) on January 12 from Korean Register (KR), which evaluates data derived from a test voyage. The AIP service is intended to assist the developers of conceptual and innovative shipbuilding solutions in the expert assessment of technical documentation at the initial design stage.
The project involves Korea Shipbuilding & Offshore Engineering (KSOE) affiliated with the Hyundai shipbuilding group, POSCO, and Hylium Industries, a developer of hydrogen technology solutions. The shipbuilding group has unveiled a new business roadmap to establish a hydrogen value chain by 2030 and develop hydrogen transport ships and create vessels with hydrogen fuel propulsion systems.
KSOE is in charge of designing a dual structure to minimize the natural vaporization of hydrogen by increasing vacuum insulation performance. POSCO develops stainless steel for storing and transporting liquid hydrogen. Hylium is responsible for manufacturing tanks. KRISO supports safety research.
For the design of a prototype, a special process has been applied to prevent ruptures at ultra-low temperatures, the research body said in an earlier announcement, adding that the inside of the tank can maintain minus 253 degrees Celsius even for long-distance operations for more than a month. A special splashboard was installed to prevent poor performance stemming from changes in the level of liquefied hydrogen and rough sailing.
A support structure with a thermal scattering function and a vapor cooling barrier was applied to improve the thermal insulation performance. New stainless steel developed by POSCO can withstand the embrittlement of metal by diffusible hydrogen in an ultra-low temperature environment. POSCO has already developed a liquefied natural gas (LNG) storage tank using high manganese steel approved by the International Maritime Organisation (IMO), a U.N. maritime safety agency.
POSCO is also involved in a separate project with the state-run Korea Institute of Machinery and Materials (KIMM), Daewoo Shipbuilding & Marine Engineering (DSME), and Korea Gas Safety Corp. (KGS) to develop a liquid hydrogen storage tank using high manganese steel, which is an alternative material for cryogenic services because it is easier to weld and has lower manufacturing costs than stainless steel.
In April 2021, Hyosung Advanced Materials, affiliated with South Korea's Hyosung Group, secured a six-year contract from Hanwha Solutions to supply high-strength carbon fiber used to reinforce hydrogen fuel tanks. Hanwha Solutions took over Cimarron Composites, an American company that has developed Neptune, a carbon fiber reinforced polymer tank capable of transporting 1,200 kg hydrogen gas in a standard 40-foot container.
In an effort to introduce eco-friendly vessels, South Korean shipbuilders have tried to adopt fuel cell technology. In September 2021, the Hyundai shipbuilding group tied up with AVL, an Austrian engineering company that provides solutions and methodologies to shape future mobility trends, to develop hydrogen fuel cells for ships by 2025.